Truck AC and HVAC repairs are essential for drivers who want to stay comfortable during long hauls. A well-functioning air conditioning system keeps the cabin cool and enhances driver efficiency. When AC or HVAC units fail, drivers face extreme temperatures, fatigue, and reduced focus. Regular maintenance prevents breakdowns and costly repairs. In this guide, we will explore common truck AC and HVAC problems, signs of failure, repair solutions, and maintenance tips.
Understanding Truck AC and HVAC Systems
Truck AC and HVAC systems regulate temperature, humidity, and air circulation. While the AC cools the air, the HVAC system ensures balanced heating, ventilation, and air conditioning. Understanding the components helps drivers and fleet managers diagnose and fix issues quickly.
Key Components of a Truck AC System
- Compressor – Pressurizes and circulates refrigerant.
- Condenser – Converts high-pressure gas into liquid and removes heat.
- Expansion Valve – Controls refrigerant flow.
- Evaporator – Absorbs heat and cools the air.
- Blower Motor – Pushes cold air into the cabin.
Key Components of a Truck HVAC System
- Heater Core – Provides warm air when needed.
- Cabin Air Filter – Removes dust, pollen, and contaminants.
- Blend Door Actuator – Adjusts temperature settings.
- Ventilation System – Maintains airflow throughout the cabin.
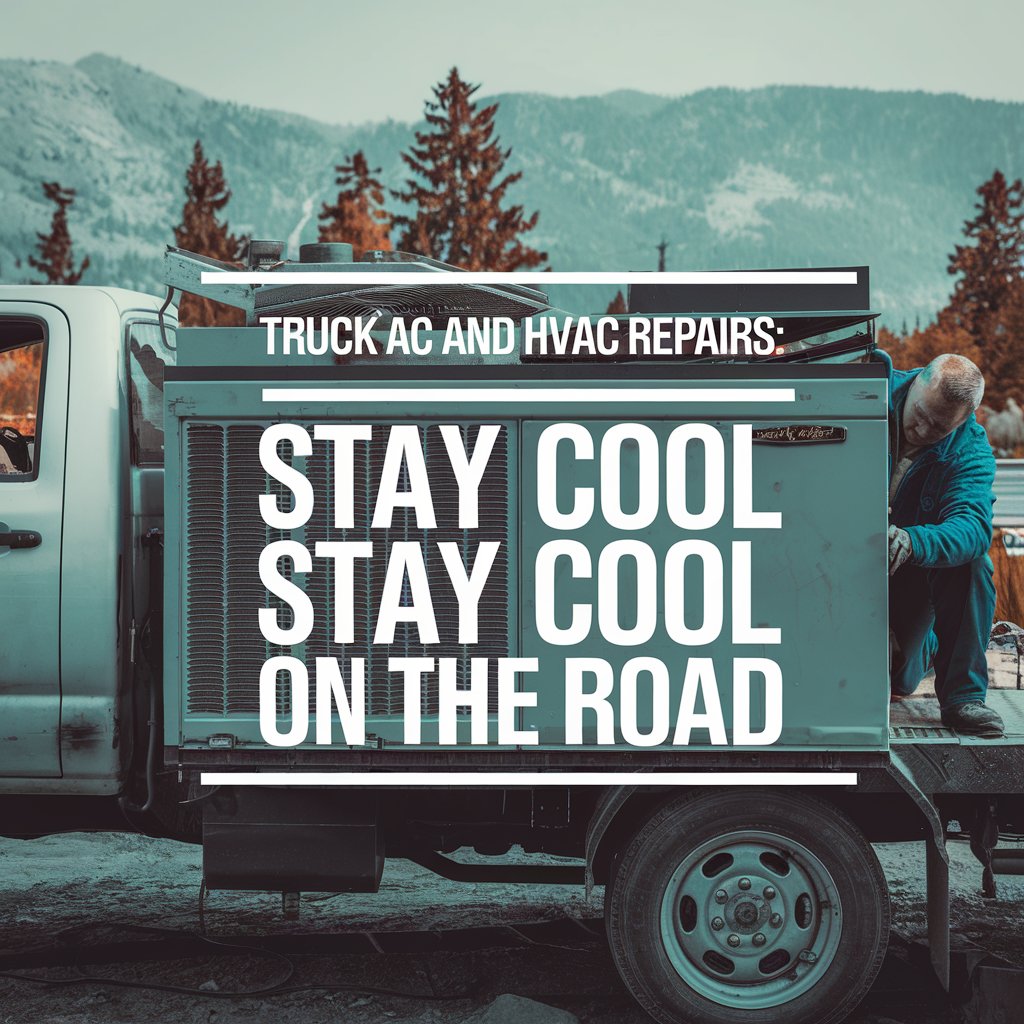
Common Truck AC and HVAC Problems
Truck AC and HVAC repairs become necessary when these systems show signs of failure. Addressing problems early prevents expensive replacements.
1. AC Blowing Warm Air
If the AC emits warm air, it may be due to:
- Low Refrigerant Levels – Leaks reduce cooling efficiency.
- Compressor Failure – A damaged compressor cannot circulate refrigerant properly.
- Clogged Condenser – Dirt and debris block airflow.
2. Weak Airflow from Vents
Poor airflow affects cooling efficiency. Common causes include:
- Dirty Cabin Air Filter – Blocks airflow and reduces cooling.
- Malfunctioning Blower Motor – Prevents air circulation.
- Leaking Ducts – Air escapes before reaching the cabin.
3. Unusual Noises from AC System
Strange sounds indicate underlying issues:
- Hissing or Bubbling – Possible refrigerant leak.
- Rattling or Grinding – Loose components or failing compressor.
- Squealing – Worn-out belts or pulleys.
4. Foul Odors from AC Vents
Unpleasant smells come from:
- Mold and Mildew – Moisture buildup in the evaporator.
- Clogged Cabin Air Filter – Traps debris and bacteria.
- Leaking Refrigerant – Causes chemical-like odors.
Truck AC and HVAC Repair Solutions
Fixing AC and HVAC problems promptly ensures comfort and prevents further damage. Below are common repair solutions for truck AC and HVAC repairs.
1. Recharge the AC System
Low refrigerant levels cause ineffective cooling. A certified technician should:
- Inspect for leaks using UV dye.
- Repair leaks before recharging.
- Refill refrigerant to manufacturer specifications.
2. Replace Faulty Components
When AC parts fail, replacing them restores performance.
- New Compressor – Required when the clutch fails.
- Condenser Cleaning or Replacement – Fixes heat dissipation issues.
- Evaporator Coil Replacement – Prevents ice buildup and weak airflow.
3. Repair or Replace the Blower Motor
A failing blower motor reduces airflow. Technicians:
- Check for power supply issues.
- Replace worn-out motor components.
- Clean or replace blower fan blades.
4. Clean or Replace the Cabin Air Filter
A dirty filter impacts air quality. Fleet operators should:
- Inspect the filter every 12,000-15,000 miles.
- Replace clogged filters.
- Use high-quality filters for better performance.
5. Fix HVAC System Malfunctions
HVAC issues affect heating and cooling. Fixes include:
- Replacing Heater Core – Resolves heating failures.
- Repairing Blend Door Actuator – Ensures proper temperature control.
- Sealing Air Duct Leaks – Restores balanced airflow.
Preventive Maintenance for Truck AC and HVAC Systems
Regular maintenance prevents major truck AC and HVAC repairs. Follow these tips to keep the system in top shape.
1. Schedule Routine Inspections
Technicians should inspect the AC and HVAC system during routine truck maintenance. Key checks include:
- Refrigerant levels
- Compressor function
- Air filter condition
- Blower motor performance
2. Keep the Condenser and Evaporator Clean
Dirt buildup affects efficiency. Maintenance steps include:
- Cleaning condenser fins regularly.
- Using compressed air to remove dust from the evaporator.
- Checking for debris blocking the airflow.
3. Test the System Before Extreme Weather
Before summer or winter, ensure AC and HVAC function properly by:
- Running the system at full capacity.
- Checking for uneven cooling or heating.
- Addressing any performance issues.
4. Monitor Refrigerant Levels
Low refrigerant leads to cooling problems. Fleet managers should:
- Use leak detection kits.
- Refill refrigerant as needed.
- Ensure refrigerant type matches manufacturer specifications.
5. Replace Worn-Out Components on Time
Delaying repairs leads to costly breakdowns. Replace parts when they show signs of failure, including:
- Cracked hoses
- Worn-out belts
- Malfunctioning actuators
Choosing a Reliable Truck AC and HVAC Repair Shop
Selecting the right repair shop ensures high-quality service. Consider these factors:
- Certified Technicians – Look for trained professionals specializing in truck AC and HVAC repairs.
- Experience with Heavy-Duty Vehicles – Ensure the shop handles commercial truck HVAC systems.
- 24/7 Emergency Services – Some repair shops offer roadside assistance for AC and HVAC issues.
- Customer Reviews – Check feedback for reliability and service quality.
Conclusion
Truck AC and HVAC repairs are crucial for driver comfort and vehicle performance. Addressing issues early prevents costly breakdowns and ensures a pleasant driving experience. Regular maintenance, timely repairs, and choosing a professional repair shop keep the AC and HVAC systems running efficiently. Stay cool on the road by prioritizing truck AC and HVAC maintenance!